UK's air-breathing SABRE rocket engine set for key tests
- Ken Ecott
- Mar 18, 2019
- 3 min read

The UK project to develop a hypersonic engine that could take a plane from London to Sydney in about four hours is set for a key demonstration. Not only would Sabre's power enable rapid, point-to-point transport inside the atmosphere, but they would also allow reusable vehicles to make the jump straight to orbit without the need for multiple propellant stages - as is the case now with conventional rockets.
The development programme of the world’s first air-breathing rocket engine has taken a significant step forward, which will lead to major testing milestones being undertaken within the next 18 months.
A three-year programme to design, build and demonstrate the core of an engine that could take a spaceplane from the ground into low-Earth orbit in a single stage looks set to pass a series of important milestones now that the European Space Agency (ESA) has approved a testing programme. The UK Space Agency (UKSA) and ESA have been reviewing the preliminary design of the demonstrator core.

Sabre engine is a concept under development by Reaction Engines Limited for a hypersonic precooled hybrid air-breathing rocket engine. The engine is being designed to achieve single-stage-to-orbit capability, propelling the proposed Skylon spaceplane to low Earth orbit.
This pre-cooler system will begin a new phase of testing in the next month or so in Colorado, US.
“The positive conclusion of our Preliminary Design Review marks a major milestone in SABRE development,” commented Mark Ford, heading ESA’s Propulsion Engineering section. “It confirms the test version of this revolutionary new class of engine is ready for implementation.”
Reaction Engines is building a test facility for the core at Wescott Venture Park in Buckinghamshire, on a site where the engines for the last generation of British-developed rockets, Blue Streak and Black Arrow, were tested in the 1950s and 60s.
Sabre, at a fundamental level, can be divided into three sections - the pre-cooler front-end; a core combustion section with a smart thermodynamic cycle to again manage heat and fluid flow; and a relatively conventional rocket arrangement at the rear.
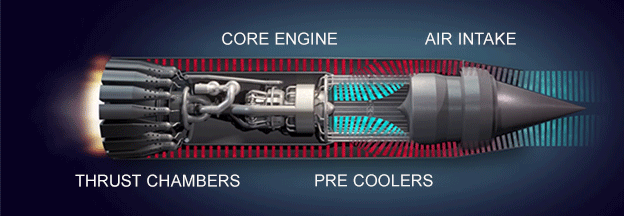
The essential innovations include a compact pre-cooler heat-exchanger that can take an incoming airstream in the region of 1,000C and cool it to -150C in less than 1/100th of a second.
Reaction Engines Limited proved the pre-cooler's efficiency at taking an ambient air stream to low temperature in 2012. Now it must do the same in a very high-temperature regime. This is the purpose of the Colorado tests.
"To have a very high-temperature, high-volume flow of air to test the pre-cooler - we needed a new facility. That is now complete," explains Shaun Driscoll, Reaction Engines Limited's programmes director.
"We will be running tests in the next month or two. We will be using re-heated aero engines to drive air through the system. We will drive air into the pre-cooler at up to 1,000C."
“One of the great advantages of the SABRE propulsion concept is that it is totally modular from both design and operational perspectives” said Richard Varvill, CTO of Reaction Engines. “Therefore it is possible to subject each of the key components of the engine to rigorous ground testing, which fully mimic the operational conditions the engine will face up to Mach 5 flight at 25km altitude.”
Over the last four years Reaction Engines has raised over £100 million from public and private sources and had secured investment from BAE Systems, Rolls-Royce and Boeing’s venture capital arm.
The complete air-breathing core demonstrator will be fully representative of the SABRE thermodynamic core cycle, fuelled by liquid hydrogen, and will contain heat-exchangers, combustion and turbomachinery modules. This milestone is expected within 18 months.
Further reading: Reaction Engines Limited Homepage
Comments