US Military testing TALOS special ops exoskeleton and plans for operational units in the 2030s
- Ken Ecott
- Nov 22, 2018
- 7 min read

Exoskeleton technologies can bring new capabilities to fighting forces and improve endurance and safety in industrial settings by reducing the effort in walking and climbing, this technology can literally help soldiers and first responders go the extra mile while carrying mission-essential equipment.
For years, U.S. Special Operations Command has been working on a suit for special operators that would essentially provide power and resiliency beyond normal human capability and it appears the project is one year away from a major milestone.
The TALOS exoskeleton is designed to shield commandos from gunfire when they are in heavy urban combat. This special situation exoskeleton system will be the first system used in combat.
The Tactical Assault Light Operator Suit, as USSOCOM formally calls it, is comprised of a base layer, an exoskeleton which is essentially a robotic skeleton, and a layer of armour. Concepts of the suit show armour from head to toe and include a complex helmet with built in situational awareness and communications capabilities.
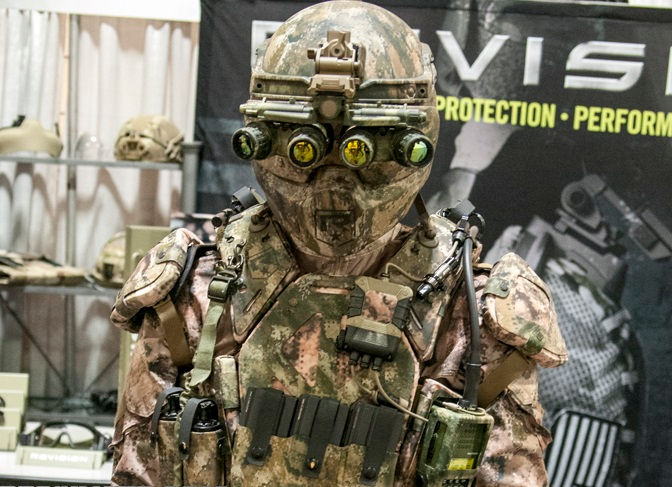
The user will be connected with his environment through enhanced situational awareness presented via multiple senses, including next-generation displays; and robust, modular, high-bandwidth communications with interoperability and compatibility across the SOF mission set and a computing platform will provide integrated, distributed information processing to serve as the central processing solution for TALOS’ integrated systems.
Soldiers with the 10th Mountain Division will be the first to test the long-awaited exoskeleton that developers say can reduce injuries, carrying loads and help troops move around the battlefield with ease.
It will take ten years before the first for major deployments of multi-mission exoskeletons. However sub-components of the system will reach a high technology readiness level by the end of the year
“There are components or aspects of the base layer, be it the thermal-state management, the constellation of sensors for different biological and physiological reading awareness that certainly have applications, useful applications, not only to the military, there are plenty of opportunities there,” said Col. James Miller, the director of the Joint Acquisition Task Force TALOS.
In fact, the program has already fielded base layer systems that help with passive thermal regulations through tubes that move fluids around the body, either warm or cold, depending on the outside environment and the heat the body is already giving off, according to Miller.
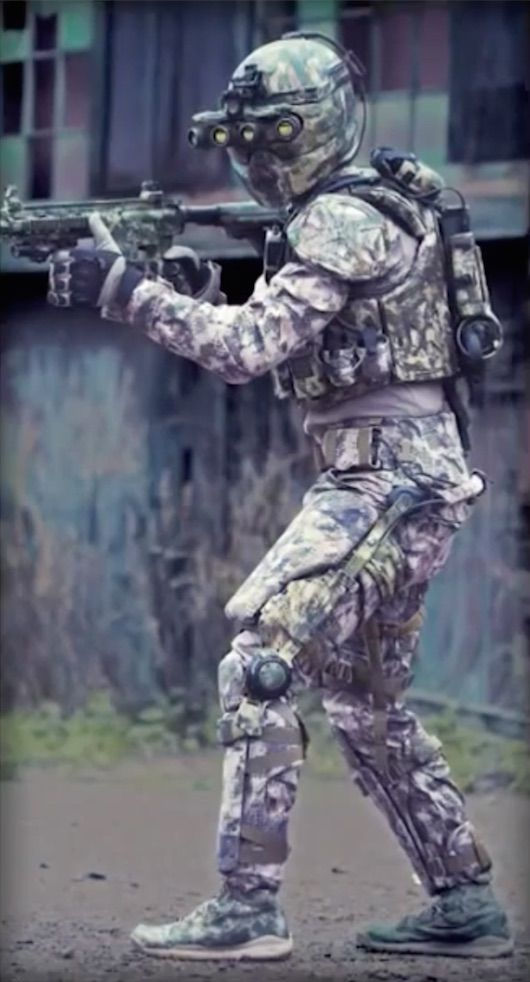
The TALOS prototype models are battery-powered hydraulic rigid exoskeletons with a bulletproof outer shell.
They have more hard armour coverage. They are like the modern version of medieval armour. Modern ceramic armour and Kevlar offer five times the protection of steel by weight.
They monitor the wearer with advanced medical technology. Sensors provide warnings of dehydration or low blood sugar.
The exoskeletons release wound-clotting foam if there is a wound.
Exoskeletons are themselves load-bearing. They help soldiers carry more and increase their mobility.
It is the only technology with the long-term potential to increase protection and improve dismounted soldier mobility.
Having exoskeletons that can operate for more than 8 to 16 hours is the main obstacle to wider adoption. There are worried potential power failures.
Improvements in power management to reduce power consumption has increased the exoskeletons endurance dramatically in the past few years. The full-body exoskeleton can operate for 8 hours of continuous walking on a level surface while carrying a 160-pound load. They allow faster movement with reduced fatigue. The load-carrying capacity of the TALOS suit is 40 pounds greater than the average load carried by dismounted troops today.
The rechargeable batteries weigh 30 pounds. A soldier could carry a spare set of batteries. This would double the suit’s endurance. Some members in the squad could have exoskeletons with internal combustion engines. They would be louder and could recharge the suit’s batteries or carrying additional batteries.
Onyx modular exoskeletons could be operational in 2021
In 2018, the Army began testing the Lockheed Martin’s ONYX exoskeleton. ONYX augments the knee joints when carrying heavy loads over uneven terrain. It uses less power than a full-body exoskeleton. The current design is able to achieve 8 to 16 hours of operation over realistic terrain. The device could be fielded as early as 2021.

ONYX conforms to the human body. Sensors distributed on the exoskeleton report speed, direction, and angle of movement to an on-board computer that drives electro-mechanical actuators at the knees.
The exoskeleton delivers the right torque at the right time to assist knee flexion and extension.
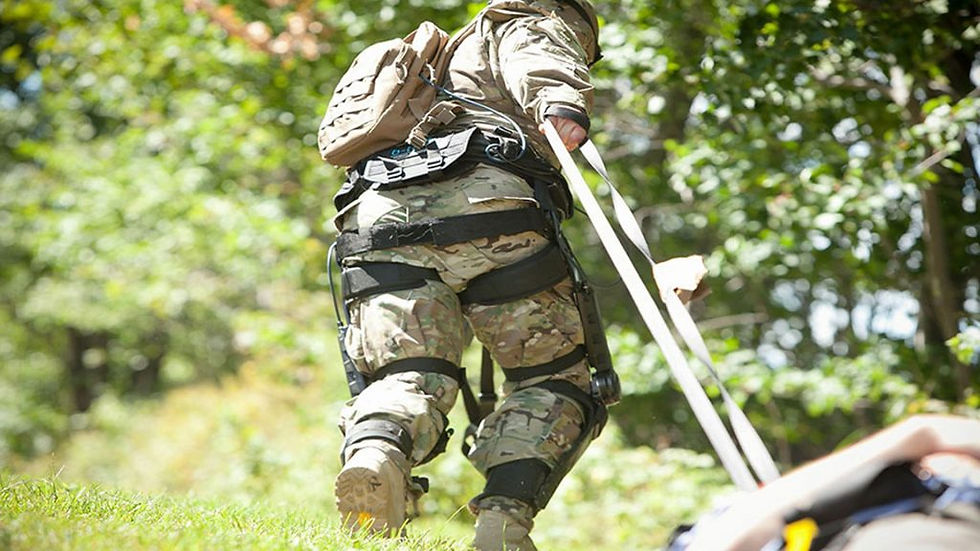
ONYX ultimately reduces the energy needed to cross terrain, squat, or kneel. These benefits are most noticeable when ascending or descending stairs or navigating inclined surfaces.
Sensors on the exoskeleton report the soldier’s speed, direction and angle of movement to an on-board computer that drives electro-mechanical actuators at the knees. The exoskeleton delivers the right torque at the right time to assist knee flex and extension.
By reducing the effort in walking and climbing, this technology can literally help soldiers and first responders go the extra mile while carrying mission-essential equipment.
Soft Exosuits
Harvard Biodesign Lab are developing next generation soft wearable robots that use innovative textiles to provide a more conformable, unobtrusive and compliant means to interface to the human body. These robots will augment the capabilities of soldiers
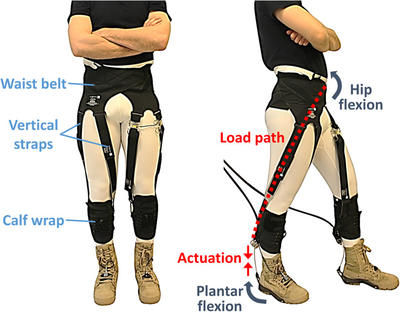
The exosuits incorporate innovative textiles that are inspired by an understanding of human biomechanics and anatomy. These wearable garments provide means to transmit assistive torques to a wearer’s joints without the use of rigid external structures.Ultimately soft exosuits can help soldiers carry 30 percent of their body mass with a 14 percent reduction in metabolic power.
They are still working to reach worthwhile improvements in carrying capacity while reducing fatigue.
Current suits use 50 to 100 watts of power. Exosuit prototypes weigh 5.5 kilograms and have smaller batteries for up to 4 hours of endurance.

The benefits vary between users. Some may see gains of 15 to 20 percent while others see no gains. Researchers need to determine how to customise the suits for everyone to see gains.
Better engines
One of the biggest problems facing engineers and designers of powered exoskeletons is the power supply. There are currently few power sources of sufficient energy density to sustain a full-body powered exoskeleton for more than a few hours.
Non-rechargeable primary cells tend to have more energy density and store it longer than rechargeable secondary cells, but then replacement cells must be transported into the field for use when the primary cells are depleted, of which may be a special and uncommon type. Rechargeable cells can be reused, but may require transporting a charging system into the field, which either must recharge rapidly or the depleted cells need to be able to be swapped out in the field, to be replaced with cells that have been slowly charging.
Internal combustion engine power supplies offer high energy output, but they also typically idle, or continue to operate at a low power level sufficient to keep the engine running, when not actively in use, which continuously consumes fuel. Battery-based power sources are better at providing instantaneous and modulated power; stored chemical energy is conserved when load requirements cease. Engines that do not idle are possible, but require energy storage for a starting system capable of rapidly accelerating the engine to full operating speed, and the engine must be extremely reliable and never fail to begin running immediately.

Liquid Piston has developed a novel rotary engine design with reduced noise. Their intended mature commercial design would be a 3-pound engine that generates 3.7 kW of power.
A hybrid gas-electric power system may be best solution. The long endurance engine would be used in most situations and the user would switch to battery-only mode when they need to be quiet.

DARPA has awarded LiquidPiston an additional $2.5 million to continue development of its 30kW X4 rotary diesel engine prototype, bringing DARPA’s total funding of the engine technology to $6 million.
When development of the fully packaged engine is complete, the 30kW X4 engine is expected to weigh just 30lbs and fit into a 10” box, while achieving 45% brake thermal efficiency – approximately an order of magnitude smaller and lighter than traditional piston diesel engines, and also 30% more efficient. The efficient, lightweight, and powerful rotary Diesel/JP-8 X4 engine offers a disruptive power solution for direct as well as hybrid electric propulsion and power generation.
* it will be about 4-30 times less volume and weight than existing engines * it will be about twice as efficient
It can be used for breakthroughs from drones, robotics and exoskeletons.
Lightweight and Compact
High power density – up to 2 HP/Lb (3.3 kW/kg) 30% smaller and lighter for spark-ignition (SI) gasoline engines Up to 75% smaller and lighter for compression-ignition (CI) diesel engines
Quiet
No poppet valves Exhaust turbulence minimized by over-expansion; no muffler required
Low-Vibration
Only two primary moving parts, optimally balanced, resulting in near-zero vibration
High-Efficiency
20% decrease in fuel consumption possible for SI gasoline engines 50% decrease in fuel consumption possible for CI diesel engines
Multi-Fuel Capable
Diesel, gasoline, natural gas, JP-8
Scalable
From 1 HP to over 1000 HP
Although the sci-fi nerd in us all is extremely excited about the possibility of storm trooper-esque soldiers I have to caution you against unrealistic expectations. There is a host of challenges still hanging over these technologies. The soft exosuit is programmed for walking, for instance, but not running. It has proven difficult to design a system that kicks in at the right time when someone is travelling over uneven terrain. Some people have an easier time adapting to the suit than others, suggesting any benefit could vary from user to user. And any final version would have to integrate with the many other parts of a military outfit.
There is still a sobering list of questions that any real-world Iron Man suit—soft or hard—will have to confront. Could using an exoskeleton cause its own set of injuries? Would the performance benefit outweigh the cost? “Say a device reduces the metabolic cost of a soldier carrying a load by 5%,” she says. “Does that translate into an operational benefit? Does it mean anything?”
Comments