Satellite builders adopting 3D printing
- Ken Ecott
- Aug 22, 2017
- 1 min read

Satellite manufacturers are turning increasingly to additive manufacturing to reduce the cost and time required to design and build spacecraft.
Space Systems Loral announced March 7 that its most complex additively manufactured part, an antenna tower with 37 printed titanium nodes and more than 80 graphite struts, is performing as intended in orbit on SKY Perfect JSAT’s JCSAT-110A satellite launched in December.
“Our advanced antenna tower structures enable us to build high-performance satellites that would not be possible without tools such as 3D printing,” Matteo Genna, chief technology officer and vice president of product strategy and development at SSL, said in SSL’s announcement.
SSL is now using the same strut-truss design methodology on other satellites it is building. That includes 13 structures SSL is designing and manufacturing. SSL is putting hundreds of 3D printed titanium structural components on its satellites per year, according to the firm’s announcement.
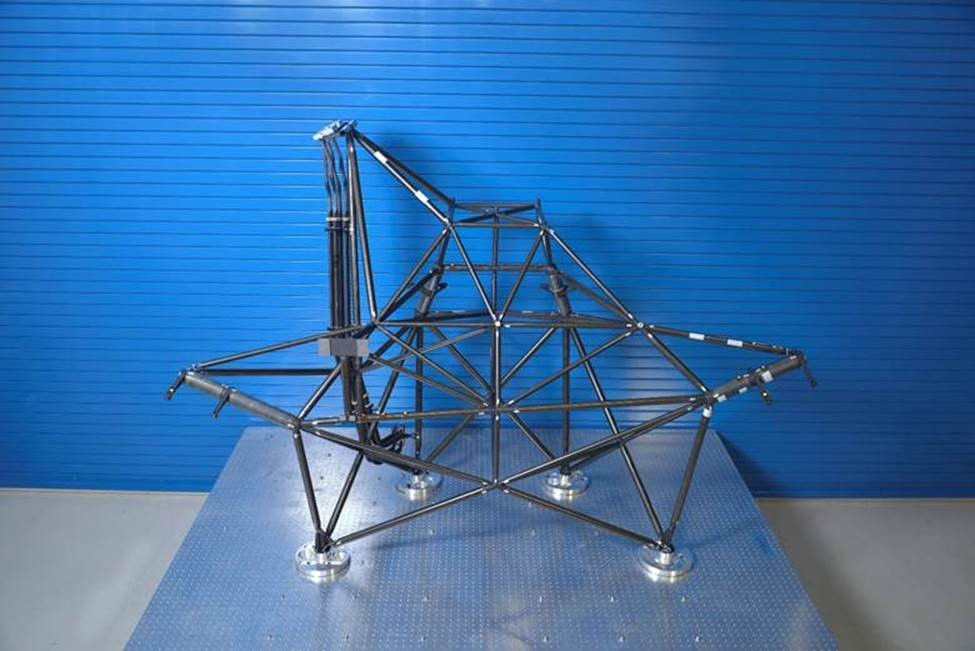
Boeing Satellite Systems International is similarly enthusiastic about additive manufacturing.
“We have satellites ready for launch that have 50 to 60 printed parts on them,” Mark Spiwak, Boeing Satellite Systems International president, said March 7 during a press briefing at the Satellite 2017 conference. “We are actively working with our suppliers on complex brackets and fittings that used to be machined parts. There is tremendous progress being made.”
Satellite manufacturers are using additive manufacturing to reduce the cost and time required to build spacecraft parts.
“The sky is the limit in how you can combine parts,” Spiwak said. “Instead of having four or five parts you can design one printed part with the same strength characteristics.”
Comments